Author |
Topic  |
B112
USA
5251 Posts |
Posted - 06/02/2009 : 07:14:02
|
Note: I am going to move this post to the "other projects" forum. I'll wait until folks notice I'm planning on moving it. |
 Michael |
 |
|
Leroy
USA
413 Posts |
Posted - 06/02/2009 : 10:43:15
|
5052 is good for corrosion resistance. It will continue to resist. Anodization would provide an extra layer of protection It can be and prolly should be anodized as well. Not aware of what method you used to clean the tank.
If there is much damage from the scale build up then the integrity should be a concern.
A gallon of gas is around 6 lbs, 6x 140 gallons is about 800 lbs. 800 lbs of fuel while wave hopping seems like it would be greater than 4 psi.
I don't think you are forced to buy a tank from the oem builder. I would venture a guess you have qualified and capable welders where you live.
A few sheets of 5052 aluminum with 5356 filler rod for a tig welder have him or her follow the dimensions of the original tank. FOB your local welding shop.
Sure if the problem is minor why not do it your self but $1000.00 to $1400.00 for a tank as you have is a $600 to $1000 too much.
If i was a bettin man, knowing the economy and all. A local working welder would love to get a job like this for Time and Materials he also gets braggin rights.
|
Edited by - Leroy on 06/02/2009 10:44:57 |
 |
|
Leroy
USA
413 Posts |
Posted - 06/02/2009 : 22:18:41
|
The HTS 2000 is a brazing rod. I looked at it a long time ago and decided against it. It may have it's uses but it looked alot like solder that almost wicked in.
I went with Muggy Weld http://www.muggyweld.com/ the Super Alloy 5 and the flux. I have a 97 Crestliner that had a 50hp 4 stroke, Mercury outboard, attached to it. Someone had rammed it into a wall and broke the motor off. I have a Lincoln Precision Tig 275 and a associates of science degree in Metallurgy. No welding experience but plenty of weld inspection and destruction experience. I know what a good weld is.
I bought the Muggy Weld Super Alloy 5 because I planned to use it. I have been so busy in the last 3 years I never got to it. Now i am laid off and the Flux is out dated. "Refrigerate when not in use" Who would have thunk it??
I emailed them and asked if it is still good after 3 years of shelf life. They said if it is liquid it is not good. I orderd a new vial of it today. I tig-ed a part of the swivel that was the least difficult to join. I will get the pics shrunk up to fit, so you can see what I'm doing.
 Whats missing?
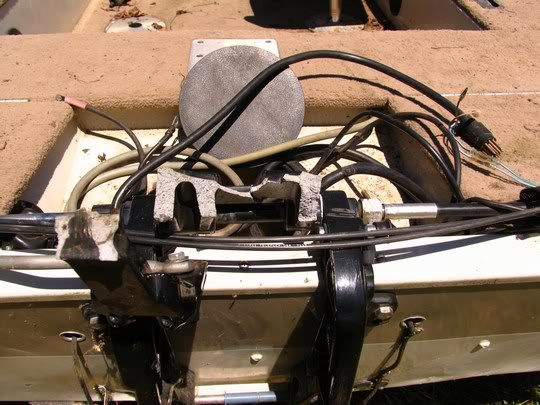 Back view
 Where the parts came from
 Left side of swivel hinge on lower right.
 Side of same
 underside
 closer
 Just a bit mor grinding
 Steering knuckle
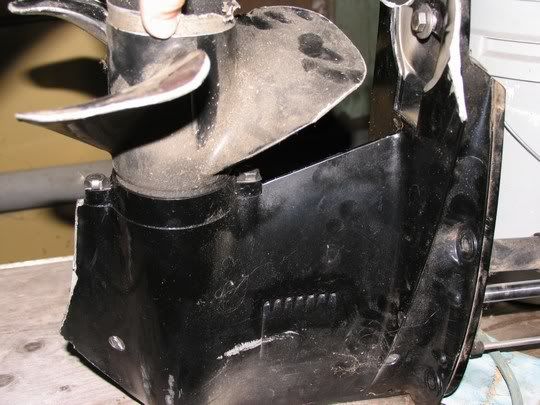 Lower end
 power head
 Anode
I used 5356 rod as filler in the areas welded. The muggy weld will be used where the cup of the tig eliminates access. I tacked the casting then routed the areas that i could reach with the cup. The other areas I will drill, rout out and back fill with Muggy Super alloy 5 weld rod. I will have to buy the rubber motor mount and the prop. The rest of it I am going to try and fix.
|
Edited by - Leroy on 06/03/2009 00:16:19 |
 |
|
B112
USA
5251 Posts |
Posted - 06/02/2009 : 22:31:03
|
Hummm... I look forward to the pictures.
I hope to show you a picture on how small the imperfection is... there is no leak yet, but a little 1/8" hole only half way through the aluminum. Unfortunately, it's on the bottom of the tank. There are a few other small imperfection areas which seem to be not even a tenth of the thickness deep. Kinda of glad you're thinking I can have it repaired. If I can find a decent tank repair place, I may lean towards that. I did read that someone had their tank repaired for $300.
Oh, the tank manufacturer told me that the 55mph limit can be exceeded when the tank is encased in foam and sits on rubber strips (which it did and will again.)
What about having a welder just put a patch on the one big spot and maybe the other two?
|
 Michael |
 |
|
Leroy
USA
413 Posts |
Posted - 06/02/2009 : 23:44:22
|
quote: Originally posted by B112
Hummm... I look forward to the pictures.
I hope to show you a picture on how small the imperfection is... there is no leak yet, but a little 1/8" hole only half way through the aluminum. Unfortunately, it's on the bottom of the tank. There are a few other small imperfection areas which seem to be not even a tenth of the thickness deep. Kinda of glad you're thinking I can have it repaired. If I can find a decent tank repair place, I may lean towards that. I did read that someone had their tank repaired for $300.
Oh, the tank manufacturer told me that the 55mph limit can be exceeded when the tank is encased in foam and sits on rubber strips (which it did and will again.)
What about having a welder just put a patch on the one big spot and maybe the other two?
If you can clean that tank so it is good enough to eat off of a welder can patch it.
By cleaning I mean chemically cleaning. It's called aluminum brightener it is an oxide eating acid. That 1/8 inch hole should prolly be drilled through and welded shut rather than covered up.
The other areas after cleaning could be patched. After that is done, if it were my tank I would put 3 thin coats of epoxy on it. I don't know if a painter would run thinned epoxy through his airless pump, but that would be the best method of application. Allowing drying times and reapply.
This activity would prevent you from ever having to pull your tank again. Visit this site for more info on epoxy coatings. http://www.epoxyproducts.com/marine.html |
Edited by - Leroy on 06/02/2009 23:46:15 |
 |
|
B112
USA
5251 Posts |
Posted - 06/03/2009 : 07:41:48
|
Leroy- Thank you. A friend of mine who's been reading this post (who welds) has complemented the excellent replies. Thank you all. I'll update this post after I either find a welder or work with my friend who was already planning on welding his tanks. Seems like salt corrosion is a common tank problem. |
 Michael |
 |
|
B112
USA
5251 Posts |
Posted - 06/05/2009 : 10:43:53
|
Greed even in this economy! I received a quote of $1200 from Vendor One for a 0.1875 tank. I was finding it difficult to understand the difference in price from vendor two (who's website link was removed from above so it doesn't "advertise them") for $772 for a 0.1875 tank to $1975. So I called Vendor two and questioned the difference in price going from $772 to $1975. They told me it was a secretarial error and they quoted me for a 1/8" tank. They didn't know the gas tank was for a "Performance Boat". I questioned that didn't they see in my original request for a quote I specified a 0.1875 gauge requirement.
Unfortunately I did not review my previous quote from Vendor One as I discovered their quote had a difference of $100 between a 0.1875 gauge and 0.25 gauge tank.
So I'm now doing the math on the cost of aluminum. The weight difference in aluminum for these tanks are 145lbs for the 0.1875 and 195lbs for the 0.25 gauge tank. Taking the price of aluminum with a high price of $0.72/lb, that's $105 and $140; can we say a $35 difference?
I'm going shoping with the quote "the boat will be repaired when it's repaired. I don't care how long it takes." Unfortunately, wife and friends do.
|
 Michael |
 |
|
Leroy
USA
413 Posts |
Posted - 06/05/2009 : 16:53:45
|
quote: Originally posted by B112
Greed even in this economy! I received a quote of $1200 from Vendor One for a 0.1875 tank. I was finding it difficult to understand the difference in price from vendor two (who's website link was removed from above so it doesn't "advertise them") for $772 for a 0.1875 tank to $1975. So I called Vendor two and questioned the difference in price going from $772 to $1975. They told me it was a secretarial error and they quoted me for a 1/8" tank. They didn't know the gas tank was for a "Performance Boat". I questioned that didn't they see in my original request for a quote I specified a 0.1875 gauge requirement.
Unfortunately I did not review my previous quote from Vendor One as I discovered their quote had a difference of $100 between a 0.1875 gauge and 0.25 gauge tank.
So I'm now doing the math on the cost of aluminum. The weight difference in aluminum for these tanks are 145lbs for the 0.1875 and 195lbs for the 0.25 gauge tank. Taking the price of aluminum with a high price of $0.72/lb, that's $105 and $140; can we say a $35 difference?
I'm going shopping with the quote "the boat will be repaired when it's repaired. I don't care how long it takes." Unfortunately, wife and friends do.
I found a sheet of 5052 H3 .1875x12x48 for $55.16 x 2 for both sides. The bottom should have a radius. So a 36x48$ 155.76 for the bottom. sides 24x24 is also 55.16 x 2 both sides.= 376.40 for brand new material. If you can get it locally. the top should be reusable. If that closely matches the dimensions. A days labor for a welder @ $30.00/hr. (376.40+240)= 616.40
$700-$800 is not too much for quality work. I'm thinking your not talking to the right people.
Going to those who are specialized is not going to be cheap.
A good Aluminum welder also makes horse trailers. A look around of those local to you will save you money. The tank builders have overhead, an independent won't have.
|
 |
|
B112
USA
5251 Posts |
Posted - 06/05/2009 : 17:52:52
|
Well as I am reviewing the quotes the cheaper ("third") vendor includes a sending unit and will epoxy coat the tank. There price without tax is $1115. I since asked the second vendor what the make of the sender they used so I can get an idea what that might cause in the difference of the tank and asked if they coat the tank. They came back with a new estimate of $1409 plus $125 totaling $1534. Boy are they missing the putt. Who knows maybe the sender is worth $400. |
 Michael |
 |
|
Leroy
USA
413 Posts |
Posted - 06/05/2009 : 23:30:53
|
quote: Originally posted by B112
Well as I am reviewing the quotes the cheaper ("third") vendor includes a sending unit and will epoxy coat the tank. There price without tax is $1115. I since asked the second vendor what the make of the sender they used so I can get an idea what that might cause in the difference of the tank and asked if they coat the tank. They came back with a new estimate of $1409 plus $125 totaling $1534. Boy are they missing the putt. Who knows maybe the sender is worth $400.
Prolly the nipple for the sender installed. The senders shouldn't be more than $60.00. Is anything wrong with your sender? Did you look at the Muggy Weld Link?
|
 |
|
B112
USA
5251 Posts |
Posted - 06/06/2009 : 06:39:51
|
quote: Is anything wrong with your sender? Did you look at the Muggy Weld Link?
Nothing wrong with my sender except for the normal boat problem of only really working when the tank is empty.
Yes, I looked at Muggy Weld Link; are you thinking I should go back to repairing this? $1400 is a lot of money for one small corrosion spot, but the time it took to remove a foamed in below deck tank was 20-30 hours. Probably 20 hours now that I know how to do it and less thinking about things. |
 Michael |
 |
|
B112
USA
5251 Posts |
Posted - 06/06/2009 : 14:22:22
|
Ok, spent the last few hours making this template for the rear bulkhead:
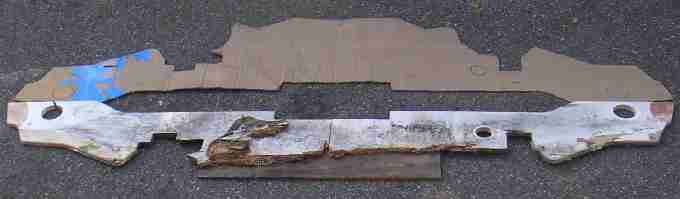 Next is the 1/4" plywood template... |
 Michael |
 |
|
Leroy
USA
413 Posts |
Posted - 06/06/2009 : 20:47:33
|
quote: Originally posted by B112
quote: Is anything wrong with your sender? Did you look at the Muggy Weld Link?
Nothing wrong with my sender except for the normal boat problem of only really working when the tank is empty.
Yes, I looked at Muggy Weld Link; are you thinking I should go back to repairing this? $1400 is a lot of money for one small corrosion spot, but the time it took to remove a foamed in below deck tank was 20-30 hours. Probably 20 hours now that I know how to do it and less thinking about things.
If you can clean it. It can be welded but the fumes need to be non existent. Some folks think sandpaper is a good thing for cleaning but it isn't when it comes to Aluminum. Also sanding will hide defects and remove unnecessary material. Pulling the sender and bench testing it, should prove it works or not. Can you wrap the tank in 8 mil poly bag then fill the hold with foam and then drop the tank in? If you have a good strong holding device for the tank after the foam. the next time you have to pull it. it should pull right out of that plastic and the foam may not have to be scraped out. ? |
 |
|
B112
USA
5251 Posts |
Posted - 06/06/2009 : 21:09:40
|
quote: Can you wrap the tank in 8 mil poly bag then fill the hold with foam and then drop the tank in?
Actually, taking out the foam was only 1/10th of the work getting the tank out. Now that I've done it, doing it again would be easy. The tough part was getting the interior disassembled, getting the bulkhead board out and thinking through the process. I'd be faster the second time around.
Now there are two schools when it comes to foaming in a tank. It's been the way to install tanks for many years now and a coast guard requirement. Supposedly you can go up in thickness (1/4") and avoid the foam, but then you still need to strap it in. There is a lot of pounding when it comes to wave in Long Island Sound, where I boat... I already broke the straps which held the tank in. I'm planning on reenforcing these straps the second time around. If I didn't have foam, the tank would have been hitting the floor boards. Could have pulled out a hose and who knows.
(School two) Lately I am reading that some boats have not been foaming in tanks and Boston Whaler stopped foaming their tanks in. The problem with foam is that if it gets wet, it puts salt water right up to a tank... making it corrode.
So I've been on the fence about putting in foam. Lately I am planning on putting the boat back together exactly as it was assembled. I'm on the fence about fixing or buying a new tank. So after a few more quotes and a little more research on repairing, I'll make the final choice. I have time as I need to finish making the bulkhead, then I am on track to assembling and the tank can come in the middle of the assembly. |
 Michael |
 |
|
Leroy
USA
413 Posts |
Posted - 06/07/2009 : 01:06:37
|
quote: Originally posted by B112
quote: Can you wrap the tank in 8 mil poly bag then fill the hold with foam and then drop the tank in?
Actually, taking out the foam was only 1/10th of the work getting the tank out. Now that I've done it, doing it again would be easy. The tough part was getting the interior disassembled, getting the bulkhead board out and thinking through the process. I'd be faster the second time around.
Now there are two schools when it comes to foaming in a tank. It's been the way to install tanks for many years now and a coast guard requirement. Supposedly you can go up in thickness (1/4") and avoid the foam, but then you still need to strap it in. There is a lot of pounding when it comes to wave in Long Island Sound, where I boat... I already broke the straps which held the tank in. I'm planning on reenforcing these straps the second time around. If I didn't have foam, the tank would have been hitting the floor boards. Could have pulled out a hose and who knows.
(School two) Lately I am reading that some boats have not been foaming in tanks and Boston Whaler stopped foaming their tanks in. The problem with foam is that if it gets wet, it puts salt water right up to a tank... making it corrode.
So I've been on the fence about putting in foam. Lately I am planning on putting the boat back together exactly as it was assembled. I'm on the fence about fixing or buying a new tank. So after a few more quotes and a little more research on repairing, I'll make the final choice. I have time as I need to finish making the bulkhead, then I am on track to assembling and the tank can come in the middle of the assembly.
The Boston Whaler may have gone to the 1/8" and they may have epoxy coated the tanks. If the tanks were epoxy coated the salt water could not get to the metal. |
 |
|
Topic  |
|